
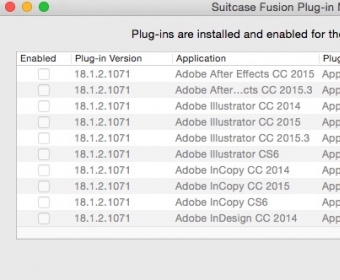
Then there is the Patch workshop which allows the user to close and delineate the surfaces, We then move in 3D with volume creation operations Create > Extrude / Revolute …”. The Sculpt workshop allows users to sculpt by drawing curves on the basis of T-Splines. However, one possible disadvantage of direct modeling is that the parts created are not necessarily functional because of the direct modeling approach (organic shapes). The star points allow to create non-rectangular polygons and thus very complex curved surfaces by limiting the quantity of polygons on the mesh.
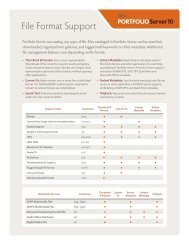
The fundamental difference between T-splines and NURBS surfaces is the presence of star points. This is a so-called surface modeling, as on other software like Rhinoceros, for example.įusion 360 operates on a spline system ( curves passing through fixed points), and more precisely T-spline. In fact, by manipulating curves and surfaces one can obtain very beautiful pieces with complex and organic shapes. Because in addition to the material thickness specifications, minimum strength and thickness concepts of each individual component must be taken into account according to users modeling.ĭirect Modeling (Design for Aesthetic Parts)ĭirect modeling offers more flexibility in terms of creativity and aesthetics. This workshop is used for measuring the mechanical strength of the materials against predetermined constraints. The Simulation workshop is particularly useful especially for functional parts. The Model workshop contains assembly functions. It is also possible to directly create volumes (cube, cylinders, spheres …) without going through the sketch. There is the Model workshop, which allows one to draw a sketch in a two-dimensional plane, which can then be transformed to 3D with the volume creation operations. Models are then further refined by parameters which can be easily modified.įreecad, Soliworks and Catia are parametric modeling software (rather engineering oriented). Parametric modeling is suitable for the modeling of parts with functional geometries (mechanical parts, such as a gear, for example). Parametric modeling (design for functional parts) Note that we distinguish in CAD two types of modeling: parametric modeling and direct modeling.

In this part, you will see the key points to create a suitable model with Fusion 360 for 3D printing. It is also important to take into account that the created file will be a virtual representation that allows 3D printers to create a physical object. Modeling for 3D printing requires attention to a number of optimal practices.įirst, there is an inherent limit to the mechanical properties of the materials used in these limits which can be tested using the software simulation model.
